As a business, we recognise that just making products that are built to last is not enough.
It is our responsibility as a business, as a manufacturer, and as individuals to take more responsibility, action and accountability for the sake of the future of our planet and our people.
That’s why we’re committed to making significant changes over the coming years to move towards being the most sustainable company that we can be. The road to this will be comprised of small changes that work together to lead to bigger, more tangible changes that have a notable impact on our company, and our world.
We keep no secrets when it comes to the quality of our products. Each product that leaves our factory is made with the utmost care and it is built to last. Much like how our company has stood the test of time, with the right care our hardware can also last a lifetime and beyond. Creating a product that can last for this long is one of the most sustainable things we have ever done, but we can and must do more.
We have created an in-house sustainability group who help us to drive forward to define and meet our goals.
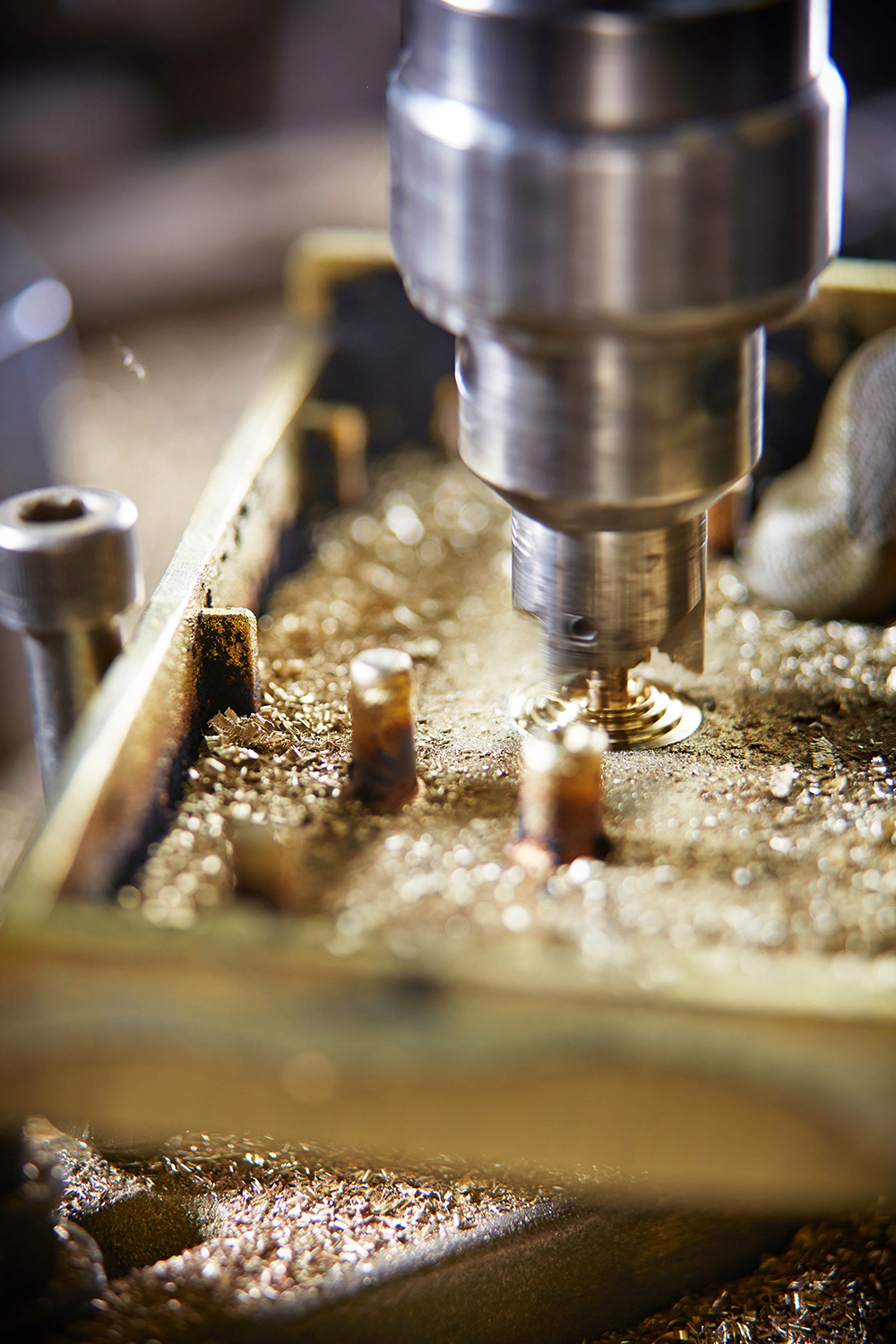
What we’re currently doing
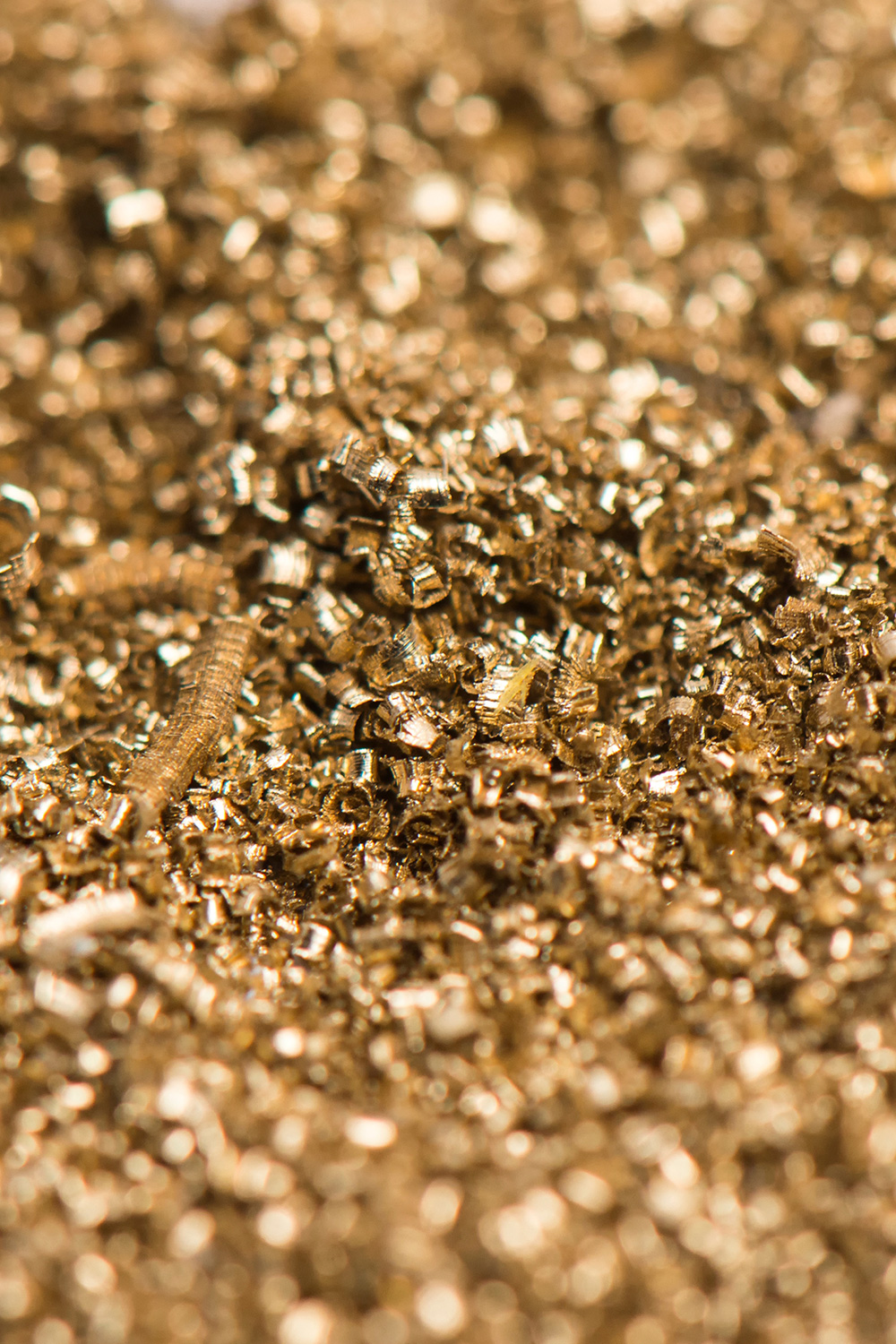
Brass recycling
Brass is infinitely recyclable which has significant environmental and economic advantages. We responsibly manage our waste by recycling 100% of the brass that does not make it into a final product. We are also looking into ways that we can recycle more brass from different stages in the product life cycle.
Refinishing
In line with our promise that our products will last a lifetime, we offer a refinishing service to update older products. This is an economical option for our customers and means that products in perfect working order don’t have to be thrown out.
Output tracking
To help us to achieve our goal of setting science-based targets, we are tracking all of our energy and water usage and looking into ways to make it more efficient. The next step is to start also measuring our waste.
We have installed LED lights across our factory reducing our energy usage by 75%, and in our factory and offices, we operate a turn off policy which relates to all lights, machinery, and taps that are not in use.
Furthermore, we are also auditing our supply chain to uncover the full picture and ensure we aren’t missing key information about our scope 3 emissions.
Positive changes we have already made
We have removed all plastic from our factory and replaced what used to be plastic cups with recycled and recyclable paper cups, and all staff have an aluminium water bottle too.
We have phased out old packaging and now use recycled and recyclable card, eco-friendly tape, and paper for all our packing.
We are experimenting with alternative, biodegradable materials for the non-brass components of some of our products
We have changed 48 filter socks on our main extraction unit in the polishing department and installed air monitors on all of our lathes. Not only does this ensure that the machinery is working properly, it also sends an alert when there is an issue or blockage which could release contaminates into the air. This has improved efficiency, but crucially, it has increased safety within our finishing department. Alongside this, we have improved a number of machines around the factory, each of which has improved efficiency, safety, or both.
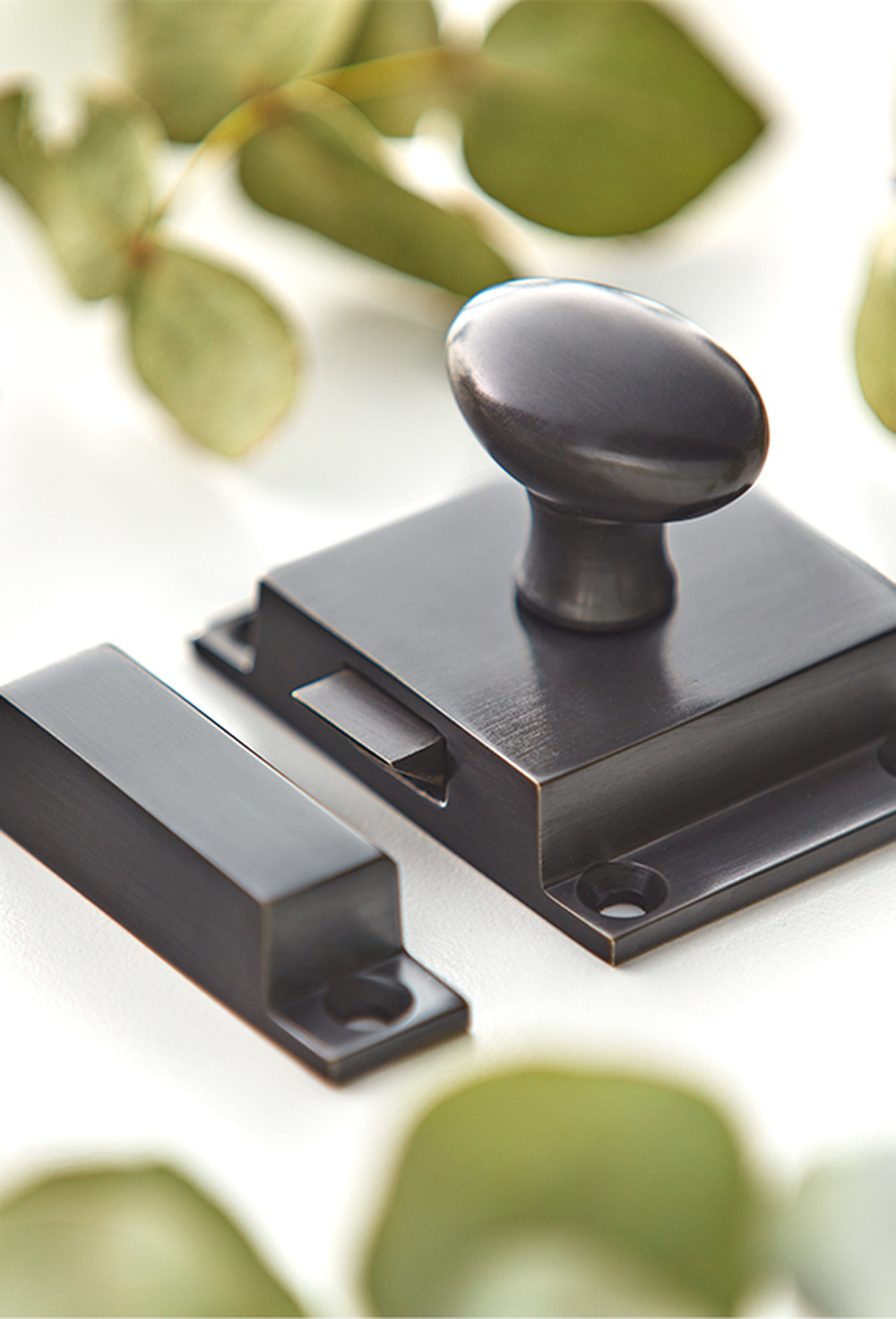